押出成形における連続加硫と釜加硫の違い・特徴を技術的に徹底解説
2025.03.24
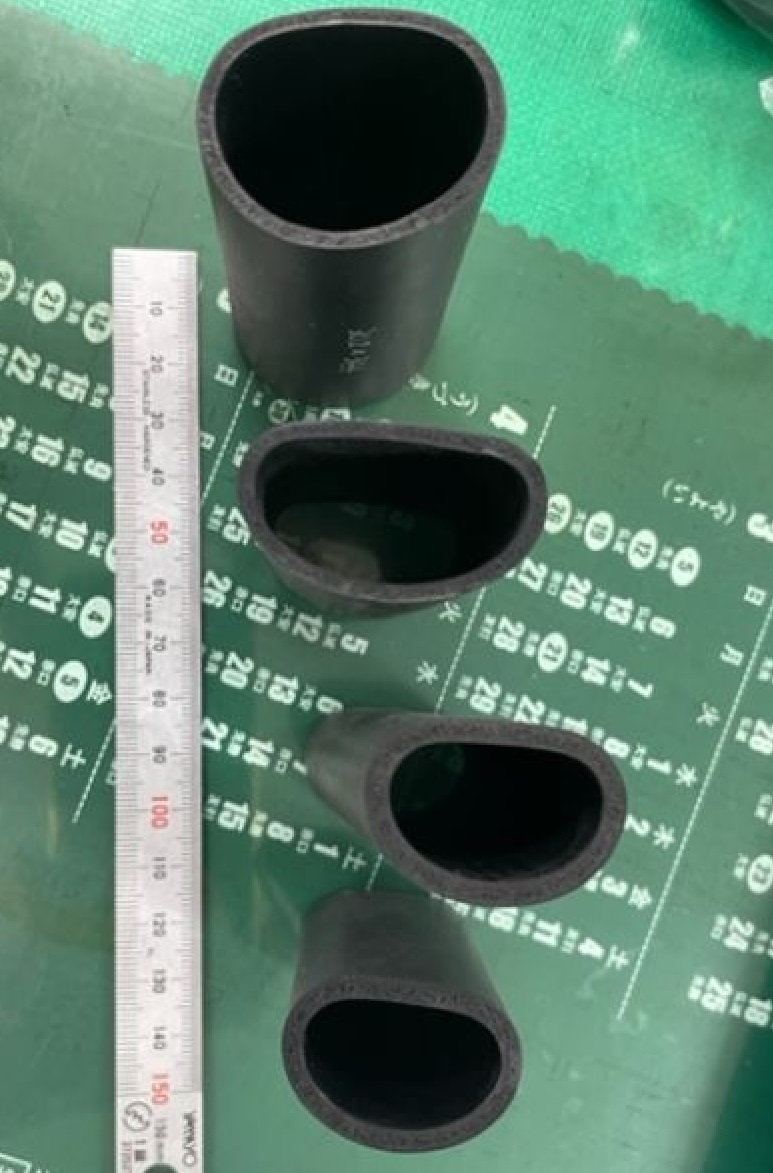
ム押出成形において、加硫(架橋)工程は製品の最終的な物性を決定づける重要なプロセスです。特にソリッドゴムの押出成形では、連続加硫と釜加硫の2つの主要な加硫方法が存在し、それぞれに特有のメリットとデメリットがあります。本記事では、これらの加硫方法の技術的な違いと適用例について詳しく解説します。
連続加硫(Continuous Vulcanization)
連続加硫は、押出成形と同時に加硫を行う方法で、高い生産性と均一な品質が求められる製品に適しています。一般的には、押出された未加硫ゴムを加熱炉や熱風炉、マイクロ波加熱炉などを通過させ、連続的に加熱することで加硫を進行させます。
メリット
- 高い生産性:連続的な加硫により、大量生産が可能です。
- 均一な品質:連続的に均一な加熱を行うため、品質のばらつきが少なくなります。
- コスト削減:連続的なプロセスにより、人件費やエネルギーコストを削減できます。ゴム調達ナビ
デメリット
- 形状の制約:複雑な形状の製品には不向きな場合があります。例えば、中空のチューブ形状を作成しようとすると、自重で潰れてしまい、楕円形になってしまったり、ヒレ部分の立ち上がり角度が安定しないなどの問題が発生します。
- 大型設備の必要性:連続的な加硫炉が必要となるため、設備が大型化する傾向があります。
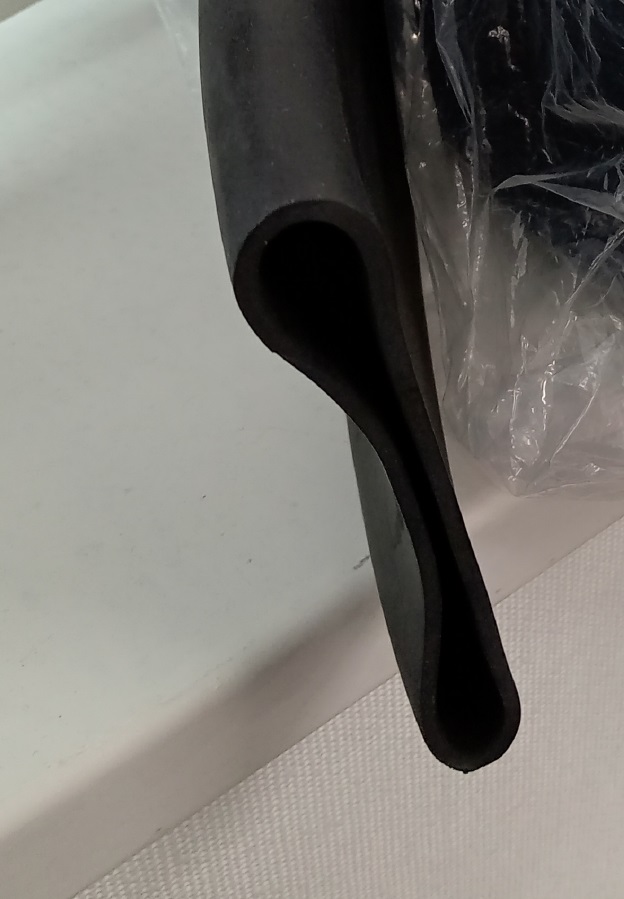
適用例
- 電線ケーブル
- ホース
- チューブ
- 建築用ガスケット
釜加硫(Batch Vulcanization)
釜加硫は、押出成形された製品を釜(加硫缶)に入れ、蒸気や熱風で加熱して加硫する方法です。バッチ処理となるため、連続加硫に比べて生産性は劣りますが、複雑な形状の製品や少量多品種の生産に適しています。
メリット
- 複雑な形状に対応:複雑な形状の製品でも均一に加硫できます。例えば、真円に近いチューブやヒレ部など、図面に近い形状を製作可能です。
- 少量多品種生産に対応:バッチ処理のため、多品種少量生産に適しています。
- 大型製品に対応:大型の製品でも加硫が可能です。
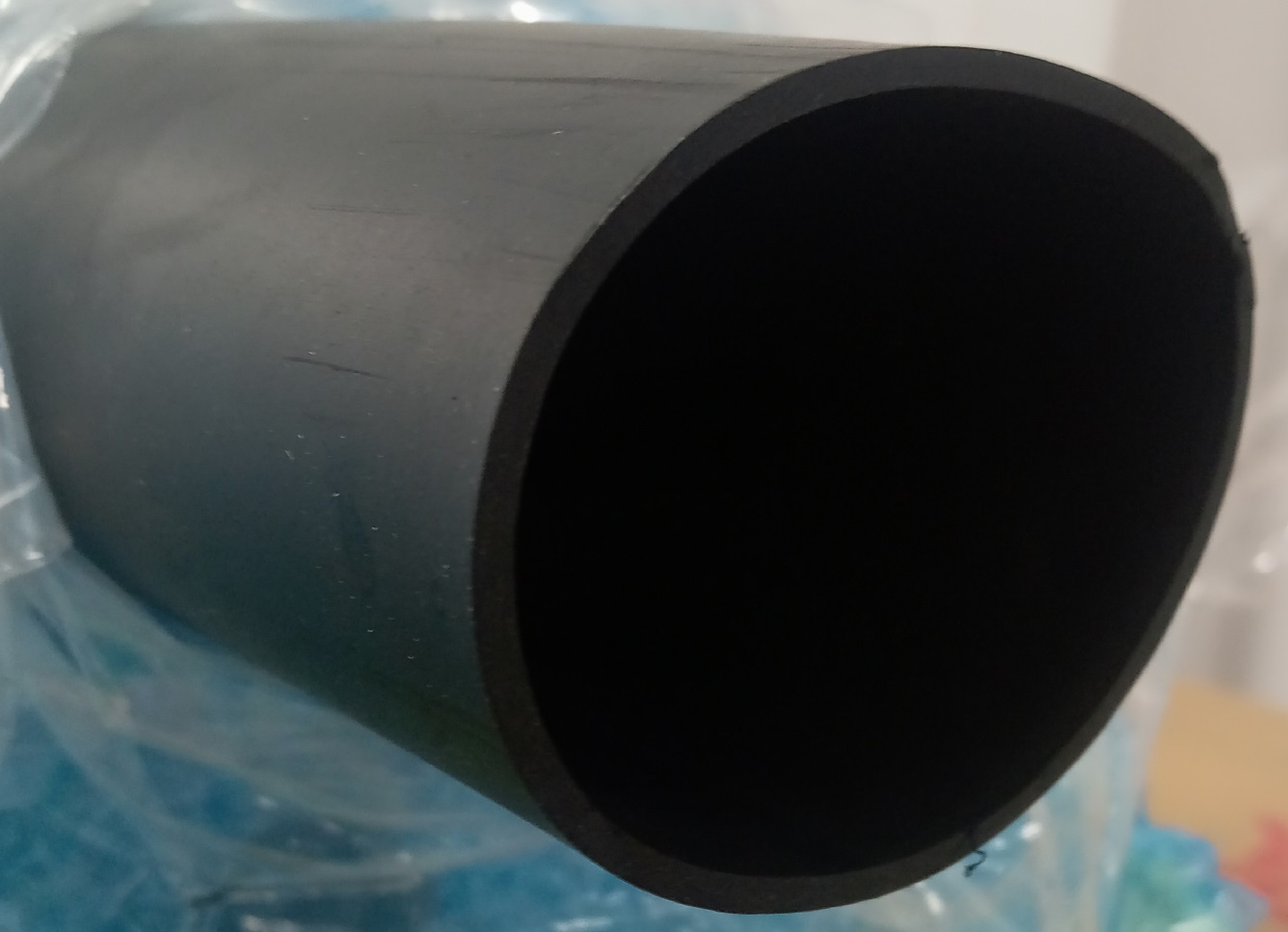
デメリット
- 低い生産性:バッチ処理のため、連続加硫に比べて生産性が劣ります。
- 品質のばらつき:加熱条件の管理が難しい場合、品質にばらつきが生じる可能性があります。
- 高いコスト:バッチ処理のため、人件費やエネルギーコストが高くなる傾向があります。
適用例
- 自動車部品
- 建築用シーリング材
- 産業用パッキン
- 大型ゴム製品
まとめ
連続加硫と釜加硫は、それぞれにメリット・デメリットがあり、製品の形状、サイズ、生産量、品質要求などに応じて適切な方法を選択する必要があります。大量生産や均一な品質が求められる場合は連続加硫が、複雑な形状や少量多品種生産には釜加硫が適しています。当社では、これらの製造方法を使い分けることで、お客様の多様なニーズに対応しております。
カテゴリー
タグ
#加工
#スポンジ
#シリコンゴムスポンジ
#遮音
#特性
#成型
#経年劣化
#NBRゴム
#対策
#金型メンテナンス
#角オビ
#軟質樹脂
#事例
#工業用ゴム
#材料販売
#切削
#熱可塑性樹脂
#製品・部品
#ゴム
#ハーフカット
#硬度
#ニュース
#対候性
#マグネット
#比較
#ニトリルゴム
#気泡緩衝材
#新製品
#2層押出
#硬質樹脂
#同等性能
#少ロット対応
#現場調査
#通い箱
#熱硬化性樹脂
#⼯程
#遮音材
#短納期対応
#導入事例
#ターポリン
#表
#マグネット入りパッキン
#材料選定
#シリコーンゴム
#発泡ポリオレフィン
#ネオロン
#断熱ホース
#両面テープ貼り
#商社
#試作相談可能
#材工
#バルブ保護 #フランジ端部 #ゴムシート #再剥離性 #輸送対策 #保管資材 #傷防止
#エラストマー
#仕⼊れ
#制振材
#加硫接着
#お役立ちコラム
#防炎
#配合
#密閉対策
#ゴム、ニュース、代替、加硫接着、金属、防振ゴム
#フッ素ゴム
#異素材
#レストン
#耐油ホース
#穴あけ
#代替材料
#コストダウン提案
#施工
#バルブ保護
#ゴム
#技術
#難燃
#CRゴムスポンジ
#包装材
#アンチモン
#独立気泡
#防音扉
#白色
#何円
#接着
#低硬度
#流体搬送材
#特注色
#材料調達
#加工相談
#帯電防止
#フランジ端部
#遮音シート
#押出成形
#長尺
#規格品
#緩衝材
#国際情勢
#半連続気泡
#分電盤
#特注
#難燃配合
#基礎知識
#在庫品
#開発製品
#エレベーター
#押出加工
#ゴム加工先探し
#静電
#ゴムシート
#梱包改善
#金属
#発泡樹脂
#即納
#難燃剤
#間仕切り
#連続気泡
#配電盤
#梱包
#アンチモン規制
#ウレタンゴム
#住友ゴム
#U字水密
#防振パッド
#ゴム部品EPDM
#モヘア
#温度管理
#再剥離
#UL94V-0
#防振ゴム
#パッキン
#ゴムスポンジ
#業界動向
#工事
#エプトシーラー
#工場設備
#製造方法
#ブチルゴム
#ポリウレタンゴム
#3Dプリンタ
#CRゴム
#リングダンパー
#ゴム部品
#モヘアシール
#空調効率
#輸送対策
#発電所
#スリッター加工
#コストダウン
#EP
#廃盤
#連続加硫
#オプシーラー
#シリコーンスポンジ
#CR
#IIR
#耐摩耗性
#受託製造
#バックアップ材
#丸型防振ゴム
#NBR
#槌屋
#猛暑
#保管資材
#耐熱性
#ギロチン加工
#導電
#耐熱
#全天シート
#窯加硫
#原反
#材料
#クロロプレン
#天然ゴム
#寝具
#劣化対策
#ミラプランク
#ばね定数
#シリコンゴム
#シュレーゲル
#化学架橋
#傷防止
#OAパネル
#プロッター加工
#梱包材
#シート
#代替
#吸音愛
#ソリッドゴム
#トムソン
#物性
#NR
#接着剤接着
#ブルーム現象
#サンペルカ
#検査
#スポンジゴム
#気密
#ポリエチレンフォーム
#発泡PEフォーム
#量産対応
#コンプレッション成型
#ポリエチレン
#無イオウ
#SVプルーフ
#吸音材
#二重押出
#抜き加工
#特長
#お次第成型
#違い
#硬化
#ミナフォーム
#少量生産
#発泡ゴム
#防虫
#PEフォーム
#クッション材
#断熱材貼り合わせ加工
#こんぽうざい
#ノンハロゲン
#PB製品
#ウレタンスポンジ
#建築
#VA提案
#長所
#ゴムチューブ
#調達
#材料置き換え
#供給
#歴史
#建築用パッキン
#ポリパイルテープ
#PEライト
#医療
#断熱材
#発泡ポリエチレン
#シリコン
#防音
#耐薬品性
#少ロット
#ゴムスポンジシート
#短所
#トムソン加工
#工場火災影響
#素材選定
#最新動向
#加硫
#防振材
#軟質塩ビシート
#三和化工
#発泡PE
#貼り合わせ
#バッカー材
#二次加工
#吸音
#耐水性
#寸法公差
#フエルトシート
#EPDM
#抜き反り
#ゴム金型成型
#TPRノブカワ
#2025年上半期
#プリント基板
#自動車部品
#軟質PVC
#イノアックコーポレーション
#屋外
#囲う
#押出成型
#テープ貼り
#制振
#材質
#押出
#在庫
#エチレンプロピレン
#タイコ状
#成形トラブル対策
#角紐
#リスクヘッジ
#材料切り替え
#配管保護材
#カーテン工事
#化工
#両面テープ